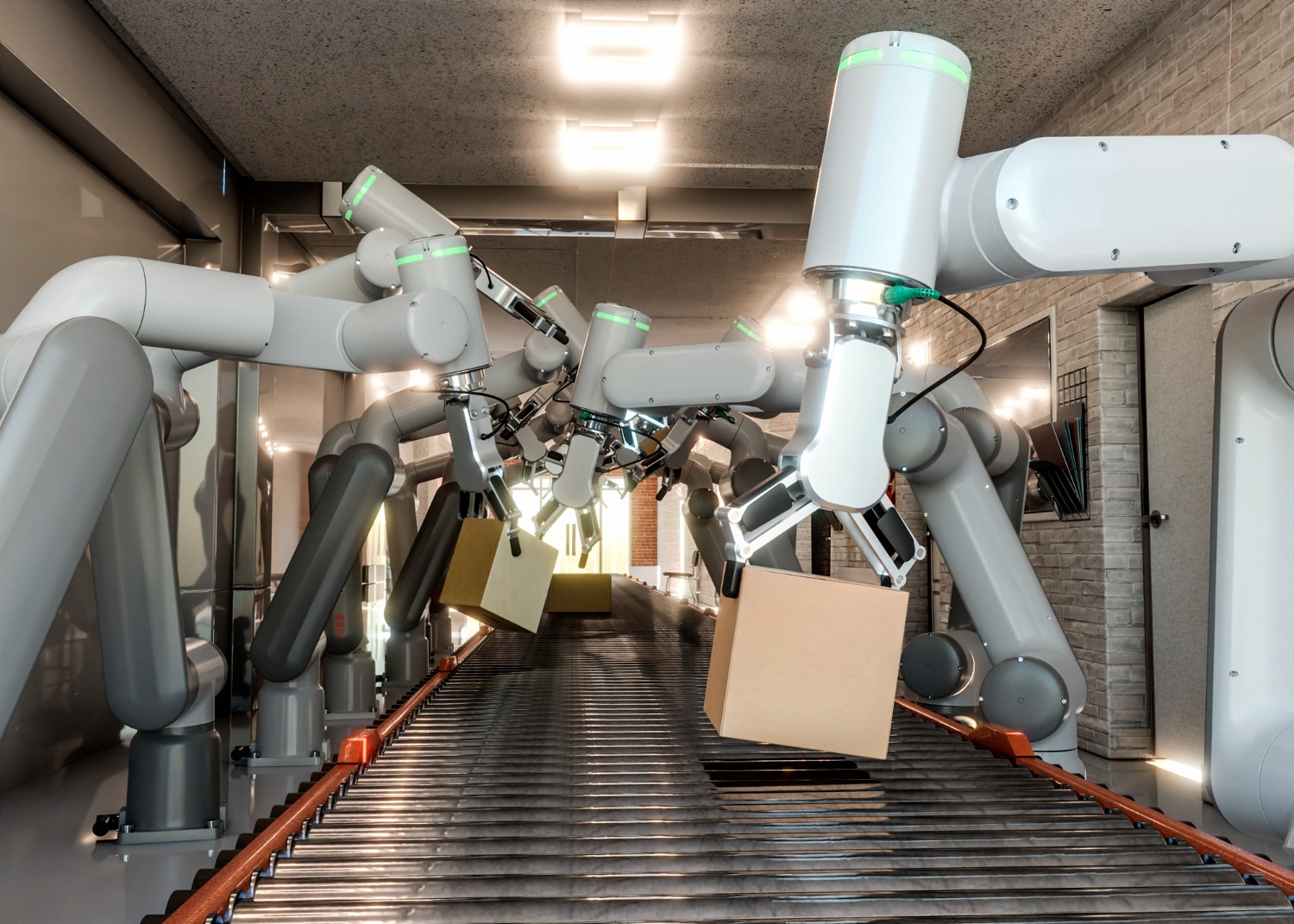
How Robots Are Changing the Manufacturing Industry
Robotics and automation are rapidly transforming the manufacturing industry. Machines powered by AI increase efficiency and point to a future in which robotic manufacturing is the norm. In this blog, we will discuss how robots are changing the way of the manufacturing industry and the advantages, challenges, and future of robotic manufacturing.
This topic is vital. As global competition increases and consumer demands evolve, manufacturers are pressured to innovate and optimise. Factory automation offers unmatched precision, speed, and reliability. But because many feel that it leads to job losses, we need to clarify these misconceptions.
Key Benefits of Automation in Factories
Enhanced Efficiency and Productivity
Automation boosts efficiency and productivity dramatically. Robots work non-stop, increasing output significantly. Unlike humans, robots don’t tire or make mistakes from repetitive tasks, ensuring consistent quality and less waste.
Improved Quality and Precision
AI robots come with advanced sensors and algorithms for high precision. This is crucial in automotive and electronics manufacturing, where precision matters most. Maintaining quality standards reduces defects and rework, leading to cost savings.
Cost Savings and Flexibility
While initial investments in robotic technology can be high, long-term savings are notable. Robots lower the need for manual labour, cutting operational costs. They can also be reprogrammed for different tasks, helping manufacturers adapt quickly to market changes.
Enhanced Safety
Automation improves workplace safety. Robots can handle dangerous tasks like welding and heavy lifting, lowering the risk of accidents. This protects workers and reduces downtime and costs.
Real-Life Applications and Data Insights
A study by the International Federation of Robotics (IFR) showed a 12% global increase in industrial robots in 2022, especially in automotive and electronics. In the UK, companies like Jaguar Land Rover and Rolls-Royce successfully integrated robotics, improving efficiency and product quality.
Step-by-Step Guide to Implementing Robotic Manufacturing
Assessing the Need for Automation
Manufacturers must assess their needs before automating. This means analysing current processes, spotting bottlenecks, and evaluating potential returns on investment.
Selecting the Right Technology
Next, choose the right robotic technology. Understand the tasks to automate and the available robotic solutions. For example, collaborative robots (cobots) work well with humans, while industrial robots excel in high-speed, precise tasks.
Designing the Automation Process
After selecting technology, design the automation process. Map out workflows, define robot and human roles, and ensure integration with existing systems.
Training and Change Management
Successful robotic manufacturing needs effective training and change management. Workers must learn to work with robots and operate new tech. Addressing resistance to change is also key for a smooth transition.
Monitoring and Optimising Performance
Post-implementation, continuously monitor and optimise robotic performance. Analyse data, find areas for improvement, and make adjustments to boost efficiency and productivity.
Additional Expert Tips & Common Mistakes to Avoid
Best Practices Beyond the Basics
- Leverage Data Analytics: Use data analytics for insights into robotic performance and to guide decisions.
- Prioritise Maintenance: Regular maintenance ensures the reliability and lifespan of robotic systems.
- Foster a Culture of Innovation: Encourage continuous improvement to unlock automation’s full potential.
Common Mistakes and Misconceptions
- Overlooking Human Factors: Human oversight remains essential even with robots handling many tasks.
- Neglecting Cybersecurity: As robotic systems connect more, cybersecurity becomes a major concern.
- Underestimating Costs: Implementation and maintenance costs can be high, so manufacturers must plan wisely.
Advanced Insights and Expert Recommendations
The Future of Robotic Manufacturing
The future of robotic manufacturing is bright. Advances in AI and machine learning will enhance robots’ capabilities. Soon, AI robots will become more autonomous, making decisions and optimising processes without human help. This will increase efficiency and flexibility in manufacturing.
Unique Industry Perspectives
Experts believe that combining robotics with technologies like the Internet of Things (IoT) and 5G will create smart manufacturing. This means real-time data exchange and seamless machine communication, leading to more efficient production systems.
Overcoming Fears
Some workers dread the day when they may be replaced by machines. Robots will transform the manufacturing sector, giving them advantages such as more efficient, better quality, and less expensive production. But effective implementation requires excellent preparation, training, and continuous improvement. The industry is constantly changing, so manufacturers must adapt by leveraging innovation to remain competitive.
The possibly of robotic manufacturing in future is very promising. Those who adjust will thrive. Manufacturers must strike a balance between using automation and keeping human workforce for an overall productive work environment.
Are you ready to embrace the future of manufacturing? The time to act is now.